Definition of a Inventory Manager
An Inventory Manager is a pivotal professional within the supply chain who specializes in overseeing and regulating the flow of goods and materials within a company. This role involves the strategic management of inventory to align with the demands of the business, ensuring optimal stock levels are maintained to meet customer needs while minimizing excess and obsolete inventory. Inventory Managers utilize a blend of analytical skills and practical knowledge to monitor stock levels, forecast demand, and coordinate with other departments such as purchasing, warehousing, and sales. Their expertise not only helps in maintaining the delicate balance between overstock and stockouts but also contributes to the overall efficiency and cost-effectiveness of the organization's operations.
What does a Inventory Manager do?
Inventory Managers play a crucial role in the operational efficiency of businesses by overseeing the flow of goods from manufacturers to warehouses and from these facilities to point of sale. They are responsible for maintaining the delicate balance between too much and too little inventory, ensuring that there is enough stock to meet demand without incurring excess costs. Their role encompasses a range of tasks from forecasting to logistics, all aimed at optimizing inventory levels and minimizing costs.
Key Responsibilities of an Inventory Manager
- Developing and implementing inventory control systems and practices to ensure accurate stock management.
- Forecasting inventory requirements and preparing procurement schedules to maintain optimal stock levels.
- Coordinating with procurement and warehouse staff to manage inventory replenishment and ensure the timely receipt of goods.
- Conducting regular inventory audits and analyses to identify discrepancies and implement corrective measures.
- Collaborating with sales and operations teams to forecast demand and adjust inventory levels accordingly.
- Managing relationships with suppliers and negotiating contracts to secure advantageous terms.
- Overseeing the logistics of inventory distribution to various locations or departments within the organization.
- Utilizing inventory management software and technologies to track inventory movements and generate reports.
- Training and supervising inventory staff in best practices for inventory control and management.
- Developing loss prevention strategies and implementing security systems to reduce shrinkage and waste.
- Setting and managing budgets related to inventory costs, including storage, labor, and transportation.
- Ensuring compliance with industry regulations and company policies regarding inventory management.
Day to Day Activities for Inventory Manager at Different Levels
The scope of responsibilities and daily activities of an Inventory Manager can significantly vary based on their experience level. Entry-level Inventory Managers are typically focused on mastering the basics of inventory control and supporting the supply chain operations, while mid-level managers oversee more complex inventory systems and processes. Senior Inventory Managers are often involved in strategic planning and decision-making, playing a crucial role in optimizing inventory efficiency and contributing to the overall success of the organization.
Below we'll break down the evolving nature of the Inventory Manager role at each career stage.
Daily Responsibilities for Entry Level Inventory Managers
At the entry level, Inventory Managers are primarily engaged in monitoring and maintaining accurate inventory records. Their daily activities often include hands-on tasks and learning the systems and processes necessary for effective inventory management.
Tracking and updating inventory records in the management system
Performing regular stock checks and reconciling inventory discrepancies
Assisting with receiving, storing, and distributing inventory
Coordinating with purchasing and warehouse staff to ensure supply levels meet demand
Learning and applying company policies and compliance standards
Participating in inventory audits and contributing to reports
Daily Responsibilities for Mid Level Inventory Managers
Mid-level Inventory Managers take on a more strategic role, managing inventory across multiple locations and contributing to process improvements. They are responsible for analyzing inventory trends and collaborating with other departments to ensure operational efficiency.
Overseeing inventory levels and turnover across various locations
Developing and implementing inventory control procedures and best practices
Forecasting inventory needs and coordinating with suppliers for timely procurement
Utilizing inventory management software to optimize stock levels
Identifying and addressing issues in the supply chain that affect inventory
Training and supervising junior inventory staff
Daily Responsibilities for Senior Inventory Managers
Senior Inventory Managers are responsible for the strategic direction of inventory management within the organization. They focus on long-term planning, cost reduction, and enhancing the overall effectiveness of the inventory system.
Creating and executing inventory management strategies aligned with business goals
Managing relationships with vendors, suppliers, and internal stakeholders
Leading cross-functional initiatives to improve inventory accuracy and reduce waste
Analyzing market trends to anticipate changes in inventory demand
Directing the integration of new technologies and systems for inventory management
Mentoring and developing inventory management teams
Types of Inventory Managers
Inventory management is a critical aspect of supply chain operations, encompassing a range of responsibilities that ensure the right products are available at the right time and place. Different types of Inventory Managers bring specialized skills and focus to their roles, addressing various challenges within the inventory lifecycle. From managing raw materials to ensuring finished products are delivered to customers efficiently, each type of Inventory Manager plays a vital role in optimizing inventory levels, reducing costs, and improving customer satisfaction. The diversity in these roles allows for a broad spectrum of career paths within the field of inventory management, catering to the specific needs of different industries and types of products.
Warehouse Inventory Manager
Warehouse Inventory Managers are the backbone of the storage and distribution aspect of inventory management. They oversee the operations within warehouses, including the receipt, storage, and dispatch of goods. Their expertise lies in optimizing warehouse layout to maximize space utilization and efficiency. They work closely with warehouse staff to implement inventory control systems, conduct regular stock checks, and ensure safety and compliance standards are met. Their role is crucial in businesses where physical inventory is a significant component, such as retail, manufacturing, and distribution centers.
Retail Inventory Manager
Retail Inventory Managers specialize in managing inventory for retail operations, where the focus is on product availability and turnover. They are adept at forecasting demand, setting stock levels, and planning replenishments to minimize stockouts and overstock situations. These managers work closely with purchasing, sales, and merchandising teams to align inventory with sales promotions and seasonal trends. Their role is essential in ensuring that the retail business maintains a balance between inventory investment and customer satisfaction, which is critical for profitability and competitive advantage.
Manufacturing Inventory Manager
Manufacturing Inventory Managers focus on the management of raw materials, work-in-progress inventory, and finished goods within a manufacturing setting. They are responsible for coordinating with procurement, production, and logistics to ensure a smooth flow of materials through the manufacturing process. Their expertise in just-in-time (JIT) inventory principles and lean manufacturing techniques helps in reducing waste and improving production efficiency. This role is vital in industries where production lead times and material availability directly impact the ability to meet customer demand.
Supply Chain Inventory Manager
Supply Chain Inventory Managers take a holistic approach to inventory management across the entire supply chain. They are responsible for balancing inventory levels across multiple locations and stages of the supply chain to optimize overall performance. Their role involves strategic planning, forecasting, and collaboration with suppliers, logistics providers, and customers to ensure inventory availability while minimizing carrying costs. They often leverage advanced analytics and supply chain management software to make informed decisions. This role is critical in complex supply chains with global reach, where coordination and efficiency are paramount.
Service Inventory Manager
Service Inventory Managers are unique in that they manage inventory for service-based industries, such as healthcare, IT, or maintenance services. Their focus is on managing parts and equipment required to deliver services effectively. They must ensure that critical components are readily available to minimize downtime and maintain service levels. These managers often work with field service technicians and customer service teams to forecast demand for spare parts and manage reverse logistics for repairs and replacements. Their role is crucial in industries where the timely availability of inventory directly impacts service quality and customer satisfaction.
Find Inventory Manager jobs on Teal
Explore the newest Inventory Manager roles across industries, career levels, salary ranges, and more.
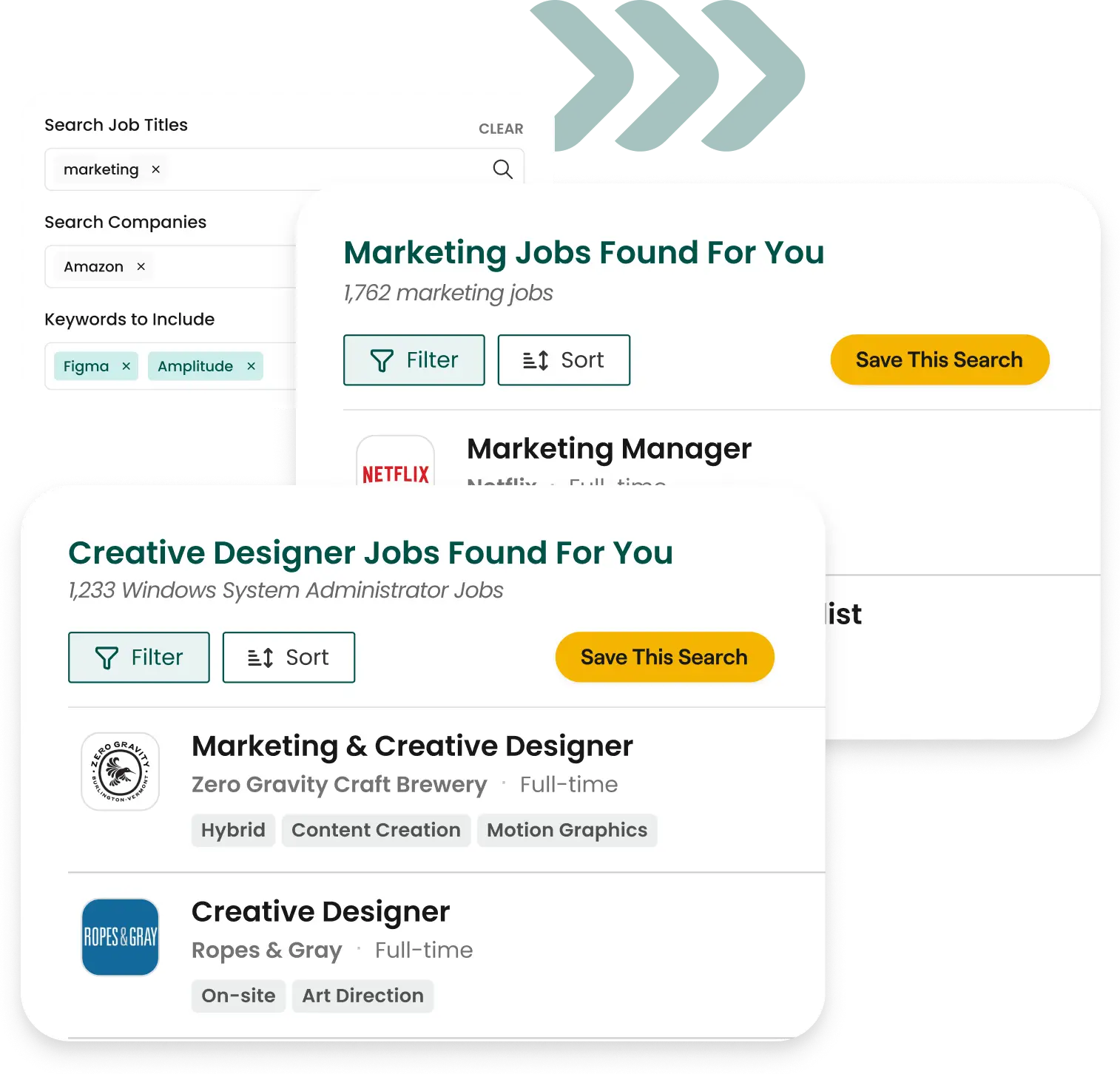
What's it like to be a Inventory Manager?
Ted Lasso
Product Manager Company
"Being a product manager is a lot like doing XYZ...you always have to XYZ"

Ted Lasso
Product Manager Company
"Being a product manager is a lot like doing XYZ...you always have to XYZ"

Stepping into the role of an Inventory Manager means entering a world where precision meets strategy. It's a profession that demands a keen eye for detail and a steadfast commitment to maintaining the delicate balance between surplus and shortage. As an Inventory Manager, you are the backbone of supply chain operations, ensuring that the right products are available at the right time and in the right quantities.
In this role, every day involves a meticulous analysis of stock levels, forecasting demand, and coordinating with suppliers and internal departments. It's a career characterized by a constant push and pull - one where analytical skills and decisive action are essential, and where your influence is directly felt in the company's operational efficiency and bottom line. For those drawn to a career that combines logistical acumen with the thrill of problem-solving, and who flourish in an environment that's structured yet dynamic, being an Inventory Manager offers a rewarding journey.
Inventory Manager Work Environment
The work environment for Inventory Managers can vary greatly depending on the industry and size of the company. Typically, it's a role that involves a combination of office work and on-site inventory checks, often within warehouses or distribution centers. The setting is collaborative, requiring constant communication with procurement teams, warehouse staff, and sales departments to ensure inventory levels align with business needs. With advancements in technology, many Inventory Managers also utilize software systems to track inventory in real-time, allowing for a more flexible and responsive approach to inventory control.
Inventory Manager Working Conditions
Inventory Managers generally work full-time, and the job can include irregular hours, especially in industries with high seasonality or during inventory audits. The role involves a significant amount of time analyzing data, monitoring inventory metrics, and planning replenishment schedules. It requires a detail-oriented mindset and the ability to remain organized under pressure. While the job can be demanding, especially when dealing with supply chain disruptions, it also offers the satisfaction of keeping business operations running smoothly and efficiently.
How Hard is it to be an Inventory Manager?
The role of an Inventory Manager can be challenging due to the need for constant vigilance over stock levels and the pressure to minimize costs while avoiding stockouts. Success in this position hinges on a combination of strong analytical skills, effective communication, and a thorough understanding of supply chain dynamics. Inventory Managers must be adept at forecasting, planning, and negotiating with suppliers, all while keeping an eye on the ever-changing market demands.
The complexity of managing a vast array of products and the need to respond swiftly to logistical challenges can make the role demanding. However, those who excel in organization and strategic planning often find the role deeply rewarding. Inventory Managers play a critical role in ensuring that businesses can meet their customers' needs, which can be a powerful motivator and a source of professional pride.
Is an Inventory Manager a Good Career Path?
Inventory Management is a crucial and respected career path within the supply chain and logistics sectors. It offers the opportunity to directly impact a company's operational effectiveness and customer satisfaction. The demand for skilled Inventory Managers is consistent, as efficient inventory control remains a cornerstone of successful business operations.
Inventory Managers often enjoy competitive salaries and the potential for career advancement into higher supply chain management roles. The role's importance across various industries, from retail to manufacturing, makes it a stable and versatile career choice. With the growth of e-commerce and global supply chains, the role of an Inventory Manager is more important than ever, presenting a career that is both challenging and full of possibilities for those who are detail-oriented and enjoy operational management.
FAQs about Inventory Managers
How do Inventory Managers collaborate with other teams within a company?
Inventory Managers are pivotal in synchronizing supply chain efficiency across departments. They work closely with procurement to monitor stock levels, align with sales to forecast demand, and coordinate with warehouse teams for inventory storage and movement. They also collaborate with finance for inventory valuation and budgeting, ensuring data accuracy and financial compliance. Regular collaboration with IT is essential to maintain inventory management systems. Their role ensures seamless operations by integrating interdepartmental objectives to optimize inventory flow and meet organizational goals.
What are some common challenges faced by Inventory Managers?
Inventory Managers grapple with maintaining optimal stock levels to prevent overstocking or stockouts, which can lead to lost sales or excess holding costs. They must also navigate the complexities of supply chain disruptions, forecast demand accurately, and implement efficient inventory tracking systems. Balancing inventory turnover with storage space constraints presents another challenge. Additionally, they must stay abreast of technological advancements and integrate them into inventory practices, all while leading teams and coordinating with other departments to ensure inventory accuracy and operational efficiency.
What does the typical career progression look like for Inventory Managers?
Inventory Managers often begin their careers in roles such as Inventory Analysts or Inventory Specialists, where they learn the nuances of stock management and supply chain operations. With experience, they progress to Inventory Managers, overseeing inventory accuracy, managing staff, and optimizing stock levels. Advancement may lead to Senior Inventory Manager positions, where they handle larger-scale operations and may influence organizational inventory strategies. The next step could be a Director of Inventory or Supply Chain Management, with responsibility for multiple warehouses or distribution centers. Ultimately, they might reach executive roles like VP of Operations or Chief Operations Officer, where they shape broader operational policies and strategies, transitioning from tactical inventory control to strategic business leadership.
Up Next
How To Become a Inventory Manager in 2024
Learn what it takes to become a JOB in 2024
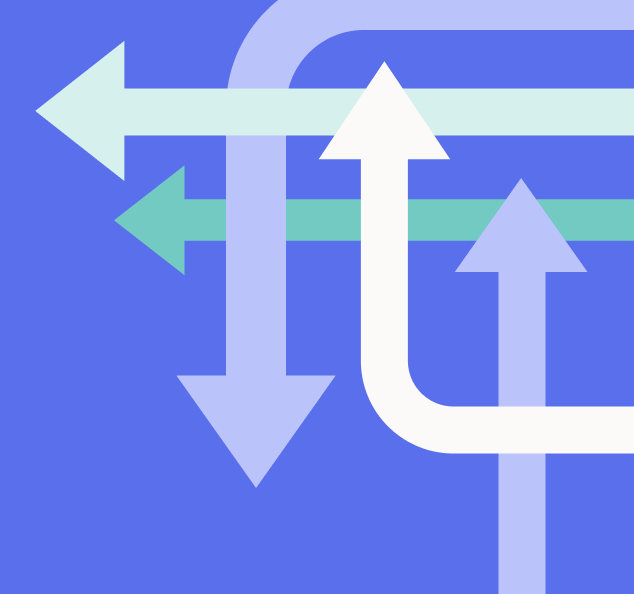