Definition of a Warehouse Operations Manager
A Warehouse Operations Manager is a pivotal figure within the logistics and supply chain network, responsible for overseeing the efficient receipt, storage, and dispatch of a wide range of goods within a warehouse setting. This role involves strategic planning and managing people, processes, and systems to ensure goods are received, stored, and shipped effectively while maintaining safety and compliance standards. The position requires a blend of leadership skills and practical knowledge, as the manager must optimize warehouse operations to meet business objectives and customer demands. As the linchpin between various stakeholders, including suppliers, customers, and employees, a Warehouse Operations Manager ensures the smooth operation of a critical component in the product lifecycle, from storage to delivery.
What does a Warehouse Operations Manager do?
Warehouse Operations Managers play a pivotal role in the logistics and supply chain process, overseeing the efficient receipt, storage, and dispatch of a wide range of goods within a warehouse setting. They are tasked with ensuring that inventory is managed effectively, warehouse operations are optimized for peak performance, and safety standards are rigorously maintained. Their role encompasses both strategic oversight and day-to-day management, requiring a balance of big-picture thinking and attention to detail to keep the warehouse running smoothly.
Key Responsibilities of a Warehouse Operations Manager
- Developing and implementing warehouse policies and procedures to ensure efficient operational flow and compliance with industry regulations.
- Overseeing and managing inventory control systems to maintain accurate stock levels and minimize loss.
- Coordinating the receipt, storage, and dispatch of goods in a timely and cost-effective manner.
- Implementing and monitoring security measures to safeguard warehouse contents and personnel.
- Conducting regular audits and inspections to ensure the warehouse meets safety and quality standards.
- Managing and optimizing warehouse layout to streamline operations and maximize space utilization.
- Leading, training, and evaluating warehouse personnel to build a high-performing team.
- Collaborating with other departments, such as procurement and transportation, to integrate logistics with company processes.
- Utilizing warehouse management systems (WMS) and other technologies to increase efficiency and accuracy.
- Forecasting future inventory requirements and planning resources accordingly.
- Resolving any operational discrepancies and addressing customer complaints related to warehouse operations.
- Preparing and managing the warehouse operational budget to control expenses and optimize resources.
Day to Day Activities for Warehouse Operations Manager at Different Levels
The scope of responsibilities and daily activities of a Warehouse Operations Manager can significantly vary based on their experience level. Entry-level managers are typically focused on the day-to-day operations and ensuring that processes are running smoothly, while mid-level managers may take on more responsibilities related to systems management and process improvement. Senior Warehouse Operations Managers often engage in strategic planning, policy development, and high-level decision-making that impacts the entire supply chain.
Below we'll break down the evolving nature of the Warehouse Operations Manager role at each career stage.
Daily Responsibilities for Entry Level Warehouse Operations Managers
At the entry level, Warehouse Operations Managers are primarily engaged in overseeing daily operations and ensuring that warehouse activities are executed efficiently. Their daily activities often include direct supervision of staff, monitoring inventory levels, and maintaining safety standards.
Supervising and directing warehouse staff and daily activities
Monitoring inventory accuracy and managing stock levels
Ensuring compliance with health and safety regulations
Coordinating receiving, warehousing, and distribution operations
Implementing operational policies and procedures
Assisting with workforce scheduling and resource allocation
Daily Responsibilities for Mid Level Warehouse Operations Managers
Mid-level Warehouse Operations Managers take on additional responsibilities that involve optimizing warehouse processes and managing a larger team. They work more independently and are often responsible for implementing improvements and managing budgets.
Developing and monitoring key performance indicators (KPIs) to improve efficiency
Managing budgets and controlling warehouse costs
Overseeing the implementation of warehouse management systems
Training and developing warehouse staff
Collaborating with other departments to integrate logistics with business systems
Identifying and implementing process improvements
Daily Responsibilities for Senior Warehouse Operations Managers
Senior Warehouse Operations Managers are responsible for strategic oversight and the broader operational health of the warehouse. They play a critical role in shaping the warehouse's contribution to the overall supply chain and company profitability.
Developing strategic plans for warehouse operations in alignment with business goals
Managing and evaluating the entire supply chain process to enhance productivity
Leading cross-functional teams to drive organizational change and efficiency
Building relationships with vendors, suppliers, and internal stakeholders
Directing the use of technology and automation to improve warehouse functions
Mentoring and developing future leaders within the warehouse operations team
Types of Warehouse Operations Managers
Warehouse operations management is a dynamic field that requires a diverse set of skills and specializations. Different types of Warehouse Operations Managers focus on various aspects of warehouse management, each bringing a distinct set of expertise to the table. This specialization allows for a range of career paths within warehouse operations, with each type of manager playing a pivotal role in the efficiency, productivity, and success of the warehouse. From overseeing inventory and logistics to managing teams and implementing technology, these managers ensure that the warehouse runs smoothly and meets the demands of the business.
Inventory Control Manager
Inventory Control Managers are specialized in managing and maintaining the accuracy and flow of inventory within a warehouse. They have a keen eye for detail and are adept at tracking stock levels, forecasting demand, and preventing overstocking or stockouts. These managers work closely with procurement and supply chain teams to optimize inventory turnover and reduce holding costs. Their role is critical in businesses where inventory management directly impacts customer satisfaction and the bottom line, such as in retail and manufacturing.
Logistics and Distribution Manager
Logistics and Distribution Managers focus on the movement of goods from the warehouse to the end customer. They are experts in transportation management, route planning, and distribution strategies. Their primary goal is to ensure timely and cost-effective delivery of products while maintaining quality standards. They collaborate with carriers, manage shipping operations, and oversee the implementation of logistics software. This role is essential in companies where the speed and reliability of delivery are competitive advantages, such as e-commerce and third-party logistics providers.
Warehouse Automation Manager
Warehouse Automation Managers are at the forefront of implementing and managing technology solutions within the warehouse. They have a strong understanding of warehouse robotics, conveyor systems, and warehouse management software (WMS). These managers are responsible for optimizing workflows, increasing throughput, and reducing manual errors through the use of technology. Their role is vital in high-volume, fast-paced warehouses that rely on automation to meet demand, such as those in the food and beverage or pharmaceutical industries.
Health and Safety Compliance Manager
Health and Safety Compliance Managers specialize in ensuring that warehouse operations adhere to occupational health and safety regulations. They are knowledgeable about safety standards, risk assessments, and emergency response planning. These managers conduct regular safety audits, provide training to staff, and implement policies to minimize workplace accidents and injuries. Their role is crucial in maintaining a safe working environment, which is particularly important in industries with hazardous materials or heavy machinery, like chemicals and automotive.
Workforce Development Manager
Workforce Development Managers concentrate on the human element of warehouse operations. They are skilled in team leadership, staff training, and performance management. These managers focus on recruiting, developing, and retaining a skilled workforce capable of meeting the operational demands of the warehouse. They create training programs, set performance metrics, and foster a positive work culture. This role is key in ensuring high productivity and employee satisfaction, which is essential in all warehouse environments, especially those experiencing growth or seasonal fluctuations.
Find Warehouse Operations Manager jobs on Teal
Explore the newest Warehouse Operations Manager roles across industries, career levels, salary ranges, and more.
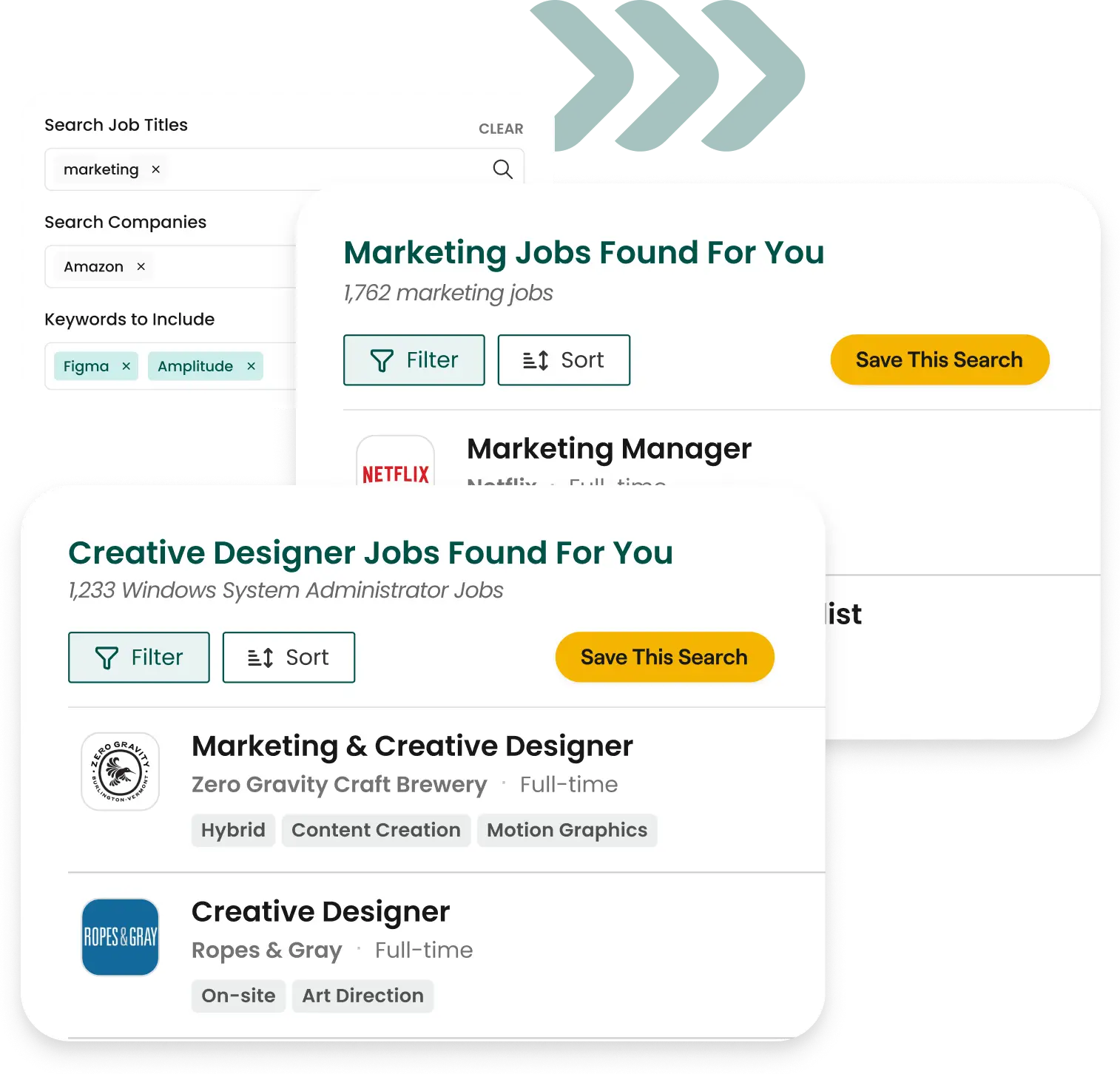
What's it like to be a Warehouse Operations Manager?
Ted Lasso
Product Manager Company
"Being a product manager is a lot like doing XYZ...you always have to XYZ"

Ted Lasso
Product Manager Company
"Being a product manager is a lot like doing XYZ...you always have to XYZ"

Stepping into the role of a Warehouse Operations Manager means entering a world where logistics, efficiency, and leadership converge. This position is the backbone of a company's distribution network, requiring a keen eye for detail and a steadfast commitment to organization. As a Warehouse Operations Manager, you are the orchestrator of various moving parts, ensuring that goods are received, stored, and dispatched accurately and on time.
In this role, every day presents a new set of challenges and opportunities to improve processes and manage a dynamic team. It's a career characterized by constant motion - one where decisiveness and strategic planning are crucial, and where your influence is directly felt in the smooth operation of the warehouse and the satisfaction of customers. For those drawn to a career that combines leadership with operational acumen, and who thrive in an environment that's both systematic and energetic, being a Warehouse Operations Manager offers a rewarding journey.
Warehouse Operations Manager Work Environment
The work environment for Warehouse Operations Managers is typically centered around the warehouse or distribution center. It's a dynamic and active setting where safety and efficiency are paramount. Managers often work on the warehouse floor, overseeing operations, and in the office, planning and coordinating logistics. The role may involve interacting with a variety of teams, including inventory, shipping, receiving, and human resources. With advancements in technology, Warehouse Operations Managers are increasingly using software systems to streamline processes, which may also involve a degree of desk work.
Warehouse Operations Manager Working Conditions
Warehouse Operations Managers usually work full-time, and the role can involve irregular hours, including early mornings, late evenings, weekends, and holidays, especially in 24-hour operations. The job requires a significant amount of time standing, walking, and sometimes lifting. It's a role that demands physical stamina, attention to detail, and the ability to manage a large team under tight deadlines. Working conditions can be challenging, particularly during peak seasons, but also rewarding, as managers play a critical role in ensuring the efficiency and effectiveness of the supply chain.
How Hard is it to be a Warehouse Operations Manager?
The role of a Warehouse Operations Manager can be demanding, with the complexity of the job varying based on the size of the warehouse, the volume of goods handled, and the specific systems in place. Managers must balance the need for operational efficiency with workforce management, often solving problems on the fly and making quick decisions. The role requires a blend of physical presence on the warehouse floor and analytical skills for planning and forecasting.
Moreover, the fast-paced nature of logistics and supply chain management means Warehouse Operations Managers must be adaptable, ready to handle unexpected challenges such as delivery delays or inventory issues. However, for those who are organized, proactive, and enjoy leading teams, the role can be extremely fulfilling. Many Warehouse Operations Managers take pride in optimizing operations, mentoring staff, and contributing to the success of the company's distribution network. It's a career path suited to those who are detail-oriented, thrive under pressure, and are passionate about logistics and supply chain management.
Is a Warehouse Operations Manager a Good Career Path?
Being a Warehouse Operations Manager is a solid career path for those interested in logistics, supply chain management, and team leadership. The role is critical to the success of any business that relies on the timely and accurate movement of goods. As e-commerce continues to grow and companies seek to optimize their supply chains, the demand for skilled Warehouse Operations Managers is likely to increase.
According to industry insights, Warehouse Operations Managers can expect competitive salaries, opportunities for career advancement, and the chance to work with cutting-edge logistics technology. The role's hands-on nature and the need for strategic logistics planning make it a challenging yet rewarding career choice. With the ongoing evolution of warehousing technologies and practices, the role of a Warehouse Operations Manager is more important than ever, offering a career that is both dynamic and essential to the global economy.
FAQs about Warehouse Operations Managers
How do Warehouse Operations Managers collaborate with other teams within a company?
Warehouse Operations Managers are pivotal in synchronizing activities across the company. They coordinate with procurement to manage inventory, align with the sales team to forecast demand, and ensure shipping aligns with customer service expectations. They also collaborate with HR for staffing needs and safety training, and with finance to control costs and budgeting. Their role is to streamline operations, ensuring efficiency and productivity while maintaining quality standards, directly impacting the company's ability to meet its strategic objectives.
What are some common challenges faced by Warehouse Operations Managers?
Warehouse Operations Managers grapple with optimizing space and inventory management amidst fluctuating supply and demand. They must ensure efficient workflow under tight deadlines, often with labor shortages or skill gaps. Safety compliance is critical, yet challenging in a fast-paced environment. Additionally, they face the pressure of integrating new technologies for process improvement while maintaining budget constraints. Effective communication, strategic planning, and adaptability are key to navigating these complex responsibilities and driving operational success.
What does the typical career progression look like for Warehouse Operations Managers?
Warehouse Operations Managers often begin their careers in entry-level positions such as Warehouse Associates, learning the nuts and bolts of inventory management, logistics, and supply chain operations. With experience, they may become Warehouse Supervisors, overseeing teams and daily operations. As Warehouse Operations Managers, they take on greater responsibilities, including strategic planning and process optimization. Advancement can lead to senior management roles such as Director of Operations, where they manage multiple warehouses or distribution centers. Ultimately, they may reach executive positions like VP of Operations or Chief Operations Officer, driving organizational efficiency and contributing to the company's strategic goals. Progression reflects a transition from operational execution to strategic leadership, with timelines varying by individual achievement and organizational opportunities.
Up Next
How To Become a Warehouse Operations Manager in 2024
Learn what it takes to become a JOB in 2024
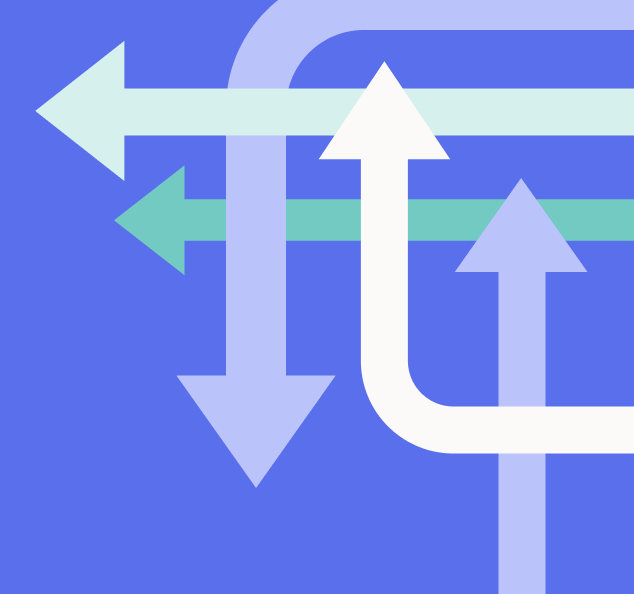