Definition of a Quality Control Manager
A Quality Control Manager is a pivotal professional within various industries who ensures that products and services meet established standards of quality, including reliability, usability, and performance. Tasked with the critical role of safeguarding consumer satisfaction and company reputation, they oversee the inspection and testing processes, manage quality assurance teams, and develop quality management systems. Their expertise lies in identifying defects, implementing corrective actions, and maintaining compliance with regulatory requirements. By continuously monitoring and evaluating the quality of products and processes, Quality Control Managers play a key role in enhancing efficiency and driving continuous improvement within an organization.
What does a Quality Control Manager do?
Quality Control Managers play a pivotal role in ensuring that products meet established standards of quality, including reliability, usability, and performance. They develop and oversee quality control systems to guarantee that products consistently satisfy customer expectations and comply with regulatory requirements. By leading a team of quality control professionals, they conduct tests and inspections, manage processes, and drive continuous improvement initiatives to enhance product quality and production efficiency.
Key Responsibilities of a Quality Control Manager
- Developing and implementing quality control procedures and systems in alignment with company objectives and industry standards.
- Overseeing the inspection of incoming materials, ensuring that they meet necessary specifications and quality benchmarks.
- Managing and guiding quality control teams to perform regular product evaluations and identify areas for quality improvement.
- Collaborating with other managers to establish quality metrics and criteria for product acceptance or rejection.
- Conducting analysis of quality control test results and providing feedback and interpretation to production teams.
- Leading root cause analysis for product defects and non-conformances and implementing corrective actions to prevent recurrence.
- Monitoring the entire production process to ensure that all procedures and activities comply with quality standards.
- Training and mentoring quality control staff on best practices, company policies, and the latest industry regulations and standards.
- Preparing and maintaining detailed reports on quality control tests, audits, and inspections for internal review and regulatory compliance.
- Working closely with suppliers and vendors to ensure quality of all third-party components, materials, and services.
- Staying abreast of new trends and advancements in quality control technologies and methodologies to drive continuous improvement.
- Ensuring that final products comply with government regulations and customer expectations, and initiating preventive measures to avoid any quality issues.
Day to Day Activities for Quality Control Manager at Different Levels
The scope of responsibilities and daily activities of a Quality Control Manager can significantly vary based on their experience level. Entry-level Quality Control Managers are typically focused on mastering the technical aspects of quality assurance processes and supporting senior staff, while mid-level managers begin to oversee teams and develop quality control strategies. Senior Quality Control Managers are involved in high-level decision-making, policy development, and play a crucial role in maintaining and enhancing the quality standards of the organization.
Below we'll breakdown the evolving nature of the Quality Control Manager role at each career stage.
Daily Responsibilities for Entry Level Quality Control Managers
At the entry level, Quality Control Managers are primarily engaged in the hands-on aspects of quality assurance and learning the standards and procedures of the industry. Their daily activities often include direct involvement in inspections, data collection, and basic analysis under supervision.
Conducting product inspections and quality tests
Documenting quality issues and compliance with regulations
Assisting with the development and implementation of quality control procedures
Collaborating with production teams to address immediate quality concerns
Participating in quality audits and contributing to corrective action plans
Engaging in continuous learning about industry standards and quality control methodologies
Daily Responsibilities for Mid Level Quality Control Managers
Mid-level Quality Control Managers take on a more supervisory role, overseeing quality control teams and processes. They are responsible for ensuring that quality standards are met consistently and are involved in the development of quality improvement initiatives.
Managing a team of quality control inspectors and technicians
Overseeing the implementation of quality control measures and monitoring their effectiveness
Analyzing quality data and reports to identify trends and areas for improvement
Collaborating with other departments to integrate quality control standards throughout the production process
Training team members on new quality control procedures and updates
Contributing to the management review of quality control systems and processes
Daily Responsibilities for Senior Quality Control Managers
Senior Quality Control Managers are responsible for the strategic direction of the quality control department. They play a key role in policy development, process improvement, and ensuring that the organization's quality standards are aligned with customer expectations and regulatory requirements.
Developing and implementing comprehensive quality control strategies and policies
Leading cross-departmental initiatives to enhance overall product quality
Directing the analysis of quality control data to inform strategic decision-making
Representing the company during external audits and regulatory reviews
Driving continuous improvement and lean initiatives within the quality control department
Mentoring and developing the next generation of quality control professionals
Types of Quality Control Managers
Quality control management is a critical aspect of ensuring that products and services meet consistent standards of excellence. Within this field, there are various types of Quality Control Managers, each with a distinct focus and set of responsibilities. These specialized roles are designed to address the unique challenges and requirements of different industries and production processes. From overseeing the quality of manufacturing processes to ensuring the compliance of pharmaceutical products, each type of Quality Control Manager plays a pivotal role in maintaining the integrity and reputation of their company's offerings.
Manufacturing Quality Control Manager
Manufacturing Quality Control Managers are pivotal in industrial production environments where they oversee the entire manufacturing process to ensure product quality and consistency. With a deep understanding of production workflows, they implement quality control standards, conduct inspections, and coordinate with production teams to correct any deviations. Their technical expertise allows them to identify potential issues before they affect the final product, making them essential in industries such as automotive, aerospace, and consumer goods manufacturing.
Food Safety Quality Control Manager
Food Safety Quality Control Managers specialize in the food and beverage industry, where they ensure that products are safe for consumption and comply with health regulations. Their role involves developing and enforcing food safety plans, auditing production processes, and managing recalls if necessary. They work closely with regulatory bodies to stay updated on food safety laws and lead their teams in maintaining the highest standards of hygiene and quality. This role is crucial in maintaining public health and consumer trust in food brands.
Pharmaceutical Quality Control Manager
Pharmaceutical Quality Control Managers are responsible for ensuring that pharmaceutical products are produced in compliance with strict industry standards and regulatory requirements. They oversee the testing of raw materials, in-process materials, and finished products to guarantee that they meet all quality specifications. Their expertise in Good Manufacturing Practices (GMP) and their ability to navigate complex regulatory landscapes are vital for the success of pharmaceutical companies and the well-being of patients.
Software Quality Control Manager
Software Quality Control Managers focus on the development and maintenance of software products. They work closely with development teams to establish quality standards, design test plans, and oversee the execution of test cases. Their role is critical in identifying bugs and ensuring that software is reliable, user-friendly, and meets customer expectations. In an industry where technology evolves rapidly, these managers are key to maintaining a competitive edge by ensuring high-quality software releases.
Supplier Quality Control Manager
Supplier Quality Control Managers play a strategic role in managing and auditing a company's supply chain. They assess supplier quality systems, conduct supplier audits, and work with vendors to resolve quality issues. Their goal is to ensure that all components and materials sourced from external suppliers meet the company's quality standards. This role is particularly important in industries where the final product is an assembly of various sourced parts, such as electronics or automotive manufacturing.
Quality Control Compliance Manager
Quality Control Compliance Managers are experts in industry standards and regulatory requirements. They ensure that their company's products and processes comply with all relevant laws and standards, such as ISO certifications. Their work involves staying abreast of regulatory changes, leading internal audits, and managing documentation for compliance purposes. This role is essential in industries that are heavily regulated, such as medical devices, aviation, and environmental services, where non-compliance can result in significant legal and financial consequences.
Find Quality Control Manager jobs on Teal
Explore the newest Quality Control Manager roles across industries, career levels, salary ranges, and more.
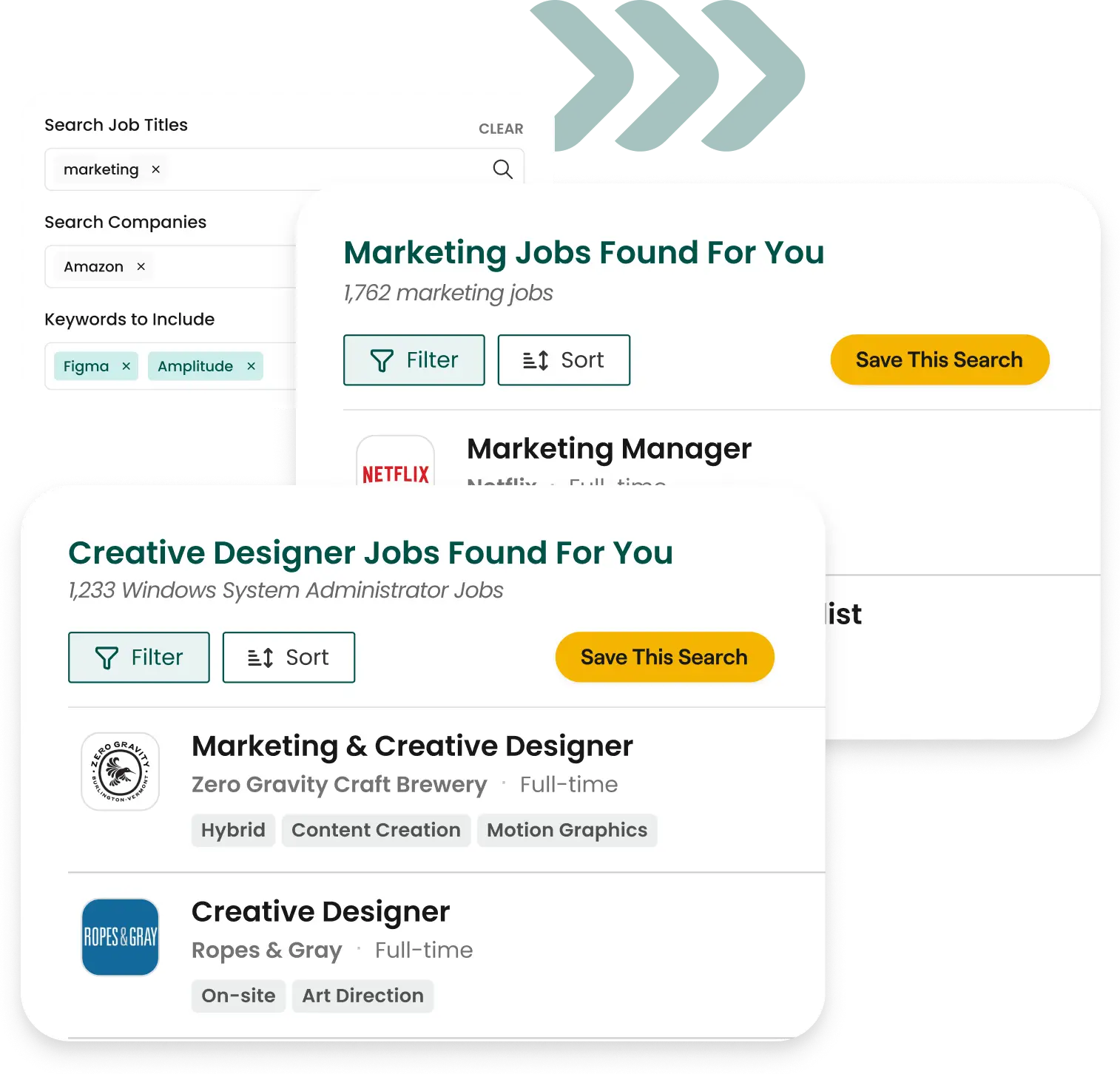
What's it like to be a Quality Control Manager?
Ted Lasso
Product Manager Company
"Being a product manager is a lot like doing XYZ...you always have to XYZ"

Ted Lasso
Product Manager Company
"Being a product manager is a lot like doing XYZ...you always have to XYZ"

Stepping into the role of a Quality Control Manager means entering a world where precision and attention to detail are paramount. It's a position that demands a meticulous eye and a steadfast commitment to ensuring that products meet or exceed established quality standards. In this role, you are the guardian of excellence, overseeing the processes that maintain product integrity and customer trust.
Every day involves a rigorous routine of monitoring production processes, analyzing quality data, and leading a team dedicated to maintaining the highest standards of quality. It's a career characterized by a structured environment - one where systematic thinking and a proactive approach to problem-solving are essential, and where your influence is directly felt in the reputation of the products and the satisfaction of the end-users. For those who take pride in upholding quality and excel in a methodical and process-driven work setting, becoming a Quality Control Manager is a rewarding and impactful career choice.
Quality Control Manager Work Environment
The work environment for Quality Control Managers is typically centered around manufacturing plants, laboratories, or warehouses, depending on the industry. It's a setting that requires a blend of on-the-floor presence and administrative oversight. Quality Control Managers often work in close collaboration with production teams, engineers, and supply chain professionals to ensure quality benchmarks are consistently met. The role may involve a significant amount of time spent in production areas, inspecting products, and processes, as well as in office settings reviewing reports and implementing quality protocols. With advancements in technology, there's also an increasing trend towards digital management of quality systems, allowing for more efficient data analysis and reporting.
Quality Control Manager Working Conditions
Quality Control Managers generally work full-time, with the possibility of overtime or irregular hours depending on production schedules and project deadlines. They are frequently on their feet, conducting inspections and audits, and may be required to work in environments that are noisy, hot, or cold, adhering to safety regulations. The role demands a high level of organization, attention to detail, and the ability to manage and prioritize multiple tasks effectively. While the job can be demanding and sometimes stressful, especially when dealing with non-compliance issues or product recalls, it also offers the satisfaction of ensuring that customers receive safe and high-quality products.
How Hard is it to be a Quality Control Manager?
Being a Quality Control Manager is challenging due to the critical nature of the role in maintaining product quality and safety. It requires a solid foundation in quality assurance principles, statistical analysis, and regulatory compliance. Quality Control Managers must possess strong leadership skills to guide their teams and enforce standards, as well as excellent communication skills to liaise with other departments and external auditors. They must be decisive, able to identify issues quickly, and implement corrective actions promptly. The job's complexity is balanced by the reward of playing a key role in protecting the brand's reputation and ensuring customer satisfaction. It's a career well-suited to those who are detail-oriented, enjoy systematic work, and take pride in contributing to the production of high-quality goods.
Is a Quality Control Manager a Good Career Path?
Quality Control Management is a vital and respected career path within various industries, including manufacturing, pharmaceuticals, food production, and more. It offers the opportunity to make a significant impact on both the quality of products and the efficiency of production processes. The demand for experienced Quality Control Managers is steady, as companies continually seek to improve their quality standards and remain compliant with industry regulations.
According to industry insights, Quality Control Managers can expect competitive salaries, opportunities for career advancement, and the potential to specialize in areas such as Six Sigma, Lean methodologies, or ISO standards. The role's focus on quality and process improvement makes it a stable and future-proof career choice. With a growing emphasis on quality across all sectors, the role of a Quality Control Manager is more important than ever, offering a career that is both challenging and filled with opportunities for personal and professional development.
FAQs about Quality Control Managers
How do Quality Control Managers collaborate with other teams within a company?
Quality Control Managers are pivotal in ensuring product excellence, interfacing with departments like R&D for specifications, production to monitor processes, and procurement to validate raw material quality. They also work with customer service to address complaints, driving continuous improvement. Their collaboration ensures standards are met across the board, maintaining the company's reputation for quality.
What are some common challenges faced by Quality Control Managers?
Quality Control Managers grapple with ensuring consistent product quality amidst varying supplier materials and manufacturing conditions. They must navigate stringent regulatory compliance, while balancing cost constraints and efficiency demands. These managers often face the challenge of implementing new quality standards across diverse teams and departments, requiring effective communication and change management skills. Additionally, they must keep abreast of technological advancements to maintain competitive edge, all while fostering a culture of continuous improvement and dealing with the pressure of immediate problem resolution.
What does the typical career progression look like for Quality Control Managers?
Quality Control Managers often begin their careers as Quality Control Technicians or Analysts, gaining hands-on experience with testing procedures and compliance standards. As they progress to Quality Control Managers, they take on supervisory roles, ensuring product quality and regulatory adherence. With further experience, they may become Senior Quality Control Managers, overseeing larger teams and strategic planning for quality initiatives. Advancement can lead to positions such as Director of Quality, where they manage quality across multiple departments or products. Ultimately, they might reach executive roles like VP of Quality or Chief Quality Officer, driving the organization's quality policies and culture. Career growth involves transitioning from operational focus to strategic leadership, with timelines varying by individual achievement and organizational opportunities.
Up Next
How To Become a Quality Control Manager in 2024
Learn what it takes to become a JOB in 2024
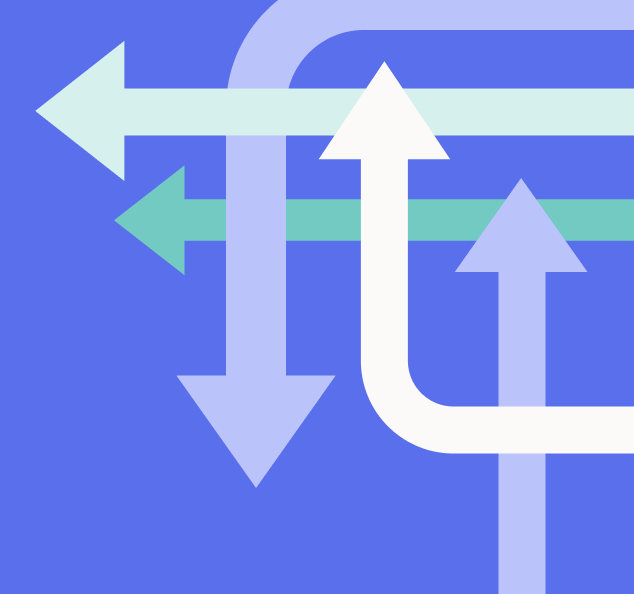