What Skills Does a Quality Control Manager Need?
In the meticulous world of quality control, the prowess of a Quality Control Manager is the cornerstone of product excellence and customer satisfaction. This role demands a specialized skill set that marries precision with leadership, ensuring that products meet stringent standards and regulatory requirements. As we edge closer to 2024, the realm of quality control is becoming increasingly complex, necessitating a deep understanding of both foundational skills and the agility to adapt to technological advancements and new methodologies.
Recognizing and honing the right skills is pivotal for those aspiring to excel as Quality Control Managers. The subsequent sections will explore the critical skills that are the bedrock of successful quality management, providing a blueprint for professionals to sharpen their capabilities and thrive in an environment where quality is paramount.
Find the Important Skills for Any Job
Discover which skills are most important to a specific job with our suite of job description analysis tools. Try it for free.
Extract Skills from Job Descriptions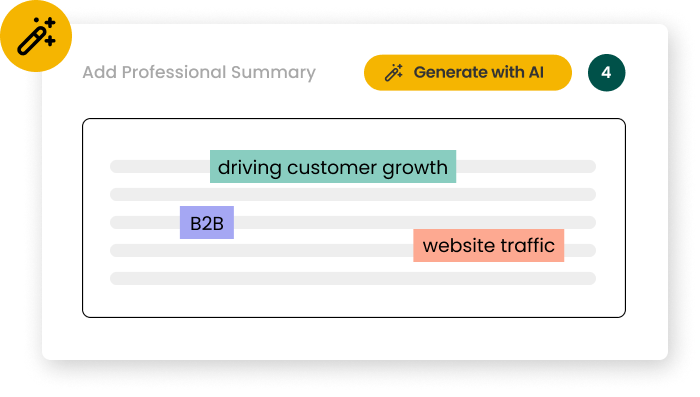
Types of Skills for Quality Control Managers
In the role of a Quality Control Manager, a comprehensive skill set is essential to ensure the highest standards of product quality and consistency. As we progress into 2024, Quality Control Managers must be equipped with a variety of skills that span technical knowledge, analytical thinking, leadership, and communication. This section delves into the critical skill types that are indispensable for Quality Control Managers, offering a guide for those looking to excel in this field and uphold the integrity of quality management processes.
Technical Proficiency and Industry Knowledge
Technical proficiency is the cornerstone of a Quality Control Manager's role. This skill set includes a deep understanding of industry standards, manufacturing processes, and quality assurance methodologies. Quality Control Managers must stay abreast of regulatory requirements and be proficient in using quality management systems and tools. This knowledge is crucial for developing and implementing quality control procedures that meet or exceed industry benchmarks.
Analytical and Problem-Solving Abilities
Quality Control Managers must possess strong analytical skills to assess product specifications and identify quality issues. This involves meticulous attention to detail and the ability to use statistical analysis to track quality trends and pinpoint root causes of defects. Problem-solving abilities are equally important, as they enable managers to devise effective solutions to quality challenges, ensuring continuous improvement in the production process.
Leadership and Team Management
Effective leadership is vital for Quality Control Managers who are responsible for guiding their teams towards maintaining quality standards. This skill encompasses the ability to motivate and train staff, manage resources efficiently, and foster a culture of quality throughout the organization. Leadership in quality control also means being able to collaborate with other departments to integrate quality practices into all aspects of the business.
Communication and Interpersonal Skills
Clear communication and strong interpersonal skills are essential for Quality Control Managers. They must be able to convey quality protocols and feedback to team members, suppliers, and customers in a clear and constructive manner. These skills also involve active listening and the ability to negotiate and resolve conflicts, ensuring that all stakeholders are aligned with the quality objectives.
Regulatory Compliance and Risk Management
Staying compliant with industry regulations is non-negotiable for Quality Control Managers. They must have a thorough understanding of compliance standards and be proactive in risk management. This skill set requires the ability to conduct audits, implement corrective actions, and maintain documentation that meets regulatory scrutiny. By effectively managing risk, Quality Control Managers safeguard the company against potential quality failures and legal issues.
Top Hard Skills for Quality Control Managers

Hard Skills
Essential skills for ensuring product excellence through meticulous quality systems, statistical analysis, and robust process improvement methodologies.
Statistical Process Control (SPC)
Quality Management Systems (QMS) Implementation
ISO Standards Compliance
Advanced Product Quality Planning (APQP)
Failure Mode and Effects Analysis (FMEA)
Root Cause Analysis
Lean Manufacturing Principles
Six Sigma Methodologies
Quality Auditing
Inspection and Testing Techniques
Top Soft Skills for Quality Control Managers

Soft Skills
Empowering teams with meticulous oversight, decisive leadership, and adaptive problem-solving to ensure unparalleled quality standards.
Attention to Detail
Leadership and Team Management
Communication and Interpersonal Skills
Problem-Solving and Critical Thinking
Adaptability and Flexibility
Time Management and Prioritization
Conflict Resolution and Negotiation
Continuous Improvement and Learning
Decision-Making
Emotional Intelligence
Most Important Quality Control Manager Skills in 2024
Advanced Analytical and Problem-Solving Abilities
As we embrace 2024, Quality Control Managers must possess advanced analytical and problem-solving skills to ensure products meet or exceed the stringent quality standards of the market. They will be tasked with dissecting complex quality issues, interpreting data from various sources, and formulating strategic solutions to prevent defects. This skill is pivotal in maintaining product integrity and customer satisfaction, and it requires a keen eye for detail and a methodical approach to troubleshooting and continuous improvement. Quality Control Managers who can adeptly navigate these challenges will be integral in upholding the reputation and success of their organizations.
Regulatory Knowledge and Compliance Expertise
In the ever-evolving landscape of industry regulations, Quality Control Managers in 2024 must have a thorough understanding of applicable laws, standards, and quality frameworks. Mastery in ensuring compliance is not just about avoiding legal pitfalls; it's about safeguarding the organization's credibility and ensuring safe, reliable products. This skill involves staying abreast of changes in regulatory requirements, interpreting them accurately, and integrating them into quality control processes. Managers who excel in regulatory knowledge and compliance will be essential in navigating the complexities of global markets and maintaining competitive advantage.
Technological Proficiency and Digital Literacy
Technological advancements continue to revolutionize quality control processes, making technological proficiency and digital literacy indispensable skills for Quality Control Managers in 2024. They must be comfortable with the latest quality management software, automation tools, and data analytics platforms. This skill extends to the ability to implement new technologies that enhance quality control measures and drive efficiency. Quality Control Managers who are technologically savvy will lead the charge in optimizing quality assurance protocols and embracing the digital transformation of the industry.
Interpersonal and Team Management Skills
The ability to lead and manage a diverse team is a critical skill for Quality Control Managers. In 2024, with the potential for remote and hybrid work environments, these managers must excel in motivating and coordinating their teams, often across different locations and cultures. This skill involves fostering a collaborative environment, resolving conflicts, and ensuring that all team members are aligned with quality objectives. Quality Control Managers with strong interpersonal and team management skills will be pivotal in building cohesive units that consistently deliver high-quality results.
Strategic Quality Planning
Strategic quality planning is a key skill for Quality Control Managers as they look ahead to 2024. This involves developing long-term plans that align with organizational goals, anticipating potential quality issues, and implementing preventive measures. A strategic approach to quality control ensures that managers are proactive rather than reactive, leading to more efficient operations and better resource allocation. Managers who can think strategically and execute quality initiatives effectively will be invaluable in driving continuous improvement and maintaining a competitive edge.
Customer-Centric Mindset
A customer-centric mindset is essential for Quality Control Managers in 2024. This skill is about understanding customer expectations and translating them into quality standards that exceed those expectations. It requires a deep empathy for the customer experience and a commitment to delivering products that not only meet but delight the end-user. Quality Control Managers who prioritize customer satisfaction in their quality control practices will contribute significantly to building brand loyalty and a strong market presence.
Effective Communication and Reporting
Effective communication and reporting skills remain vital for Quality Control Managers as they enter 2024. They must be able to convey complex quality data and insights in a clear and actionable manner to stakeholders at all levels. This skill is not only about transparency but also about empowering decision-makers with the information needed to make informed choices about product quality and process improvements. Quality Control Managers who are adept communicators will facilitate better understanding and collaboration across departments, enhancing the overall quality culture within their organizations.
Resilience and Change Management
Resilience and change management are crucial traits for Quality Control Managers facing the dynamic and sometimes volatile landscape of 2024. The skill to adapt to new challenges, embrace innovative quality practices, and lead teams through change is more important than ever. This involves not only managing one's own response to change but also supporting team members and maintaining productivity during transitions. Quality Control Managers who demonstrate resilience and effective change management will ensure that their organizations remain agile and responsive to the evolving demands of quality assurance.
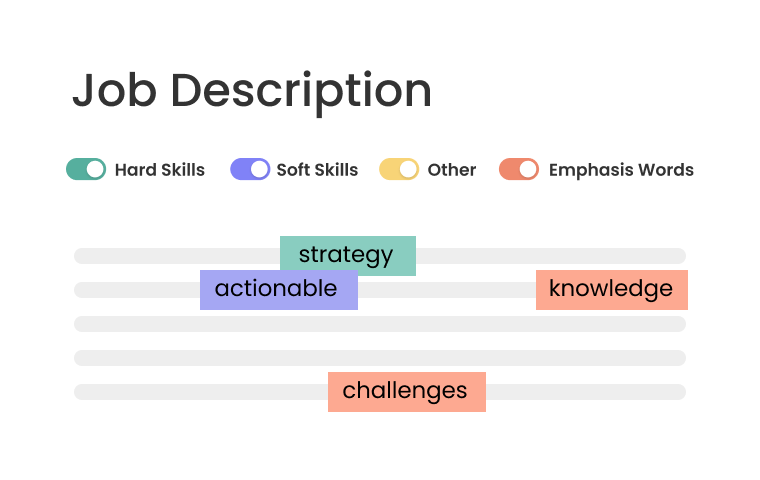
Show the Right Skills in Every Application
Customize your resume skills section strategically to win more interviews.
Customize Your Resume with AIQuality Control Manager Skills by Experience Level
The skillset required for a Quality Control Manager evolves significantly as they advance through their career. At the entry-level, the focus is on grasping the fundamentals of quality assurance and developing a keen eye for detail. As they progress to mid-level management, the emphasis shifts towards process improvement and team leadership. At the senior level, strategic planning and organizational influence become key. Recognizing which skills are essential at each stage is crucial for Quality Control Managers to effectively navigate their career progression and ensure they are equipped with the necessary competencies for success at every tier.
Important Skills for Entry-Level Quality Control Managers
Entry-level Quality Control Managers must have a solid understanding of quality standards and testing methodologies. They should be adept at using quality control tools and possess strong attention to detail to identify defects and inconsistencies. Skills in documentation and reporting are also vital, as is the ability to work closely with production teams to communicate quality issues. These foundational skills are crucial for ensuring products meet the required specifications and for supporting the quality control process within the organization.
Important Skills for Mid-Level Quality Control Managers
Mid-level Quality Control Managers need to expand their skill set to include process optimization and team management. They should be proficient in statistical analysis and capable of interpreting data to make informed decisions about quality control processes. Leadership skills become increasingly important, as they are often responsible for supervising quality control teams and training new staff. Additionally, they must be able to collaborate effectively with other departments to integrate quality management systems into the broader operational framework of the company.
Important Skills for Senior Quality Control Managers
Senior Quality Control Managers are expected to have a strategic approach to quality management, with a focus on long-term quality improvement and organizational excellence. They should have a strong command of regulatory compliance and risk management, as well as the ability to lead cross-functional initiatives that enhance product quality across the company. Advanced skills in change management and the ability to influence company culture towards a quality-centric ethos are essential. At this level, they play a critical role in shaping the quality vision and policies that drive the organization's success in the marketplace.
Most Underrated Skills for Quality Control Managers
In the realm of Quality Control Management, certain skills are essential yet often overlooked. These underrated abilities are the unsung heroes that contribute significantly to the success and efficiency of quality control processes.
1. Active Listening
Active listening is a critical skill for Quality Control Managers, as it enables them to fully understand feedback, concerns, and suggestions from both their team and clients. This deep level of understanding is essential for identifying the root causes of quality issues and for fostering a culture of continuous improvement.
2. Conflict Resolution
The ability to resolve conflicts effectively is vital in maintaining a cohesive team and ensuring smooth operations. Quality Control Managers with this skill can navigate disagreements within their team or with other departments, leading to more collaborative solutions and a stronger focus on quality outcomes.
3. Statistical Analysis
While technical know-how is expected, the power of statistical analysis is often underrated in quality control. Managers adept in this area can predict trends, understand variability, and make data-driven decisions that significantly improve product quality and consistency, ultimately saving the company time and resources.
How to Demonstrate Your Skills as a Quality Control Manager in 2024
In the ever-evolving field of quality management, Quality Control Managers in 2024 must exhibit their expertise through proactive engagement and visible results. To demonstrate a deep understanding of quality standards and regulatory compliance, one can lead workshops or publish articles on the latest industry developments.
Showcasing analytical skills is crucial; consider presenting case studies of successful process improvements or defect reduction initiatives at conferences or webinars. Collaborate with supply chain partners to illustrate your ability to manage quality across the lifecycle of a product.
To display leadership and problem-solving abilities, mentorship of junior staff or the orchestration of interdepartmental quality circles can be very effective. Engaging in advanced training or obtaining new certifications in quality management systems will not only enhance your skill set but also serve as a testament to your commitment to excellence in the field.
How You Can Upskill as a Quality Control Manager
In the dynamic field of quality control management, staying at the forefront of industry standards and methodologies is crucial. As we step into 2024, Quality Control Managers must cultivate an upskill/improvement mentality to ensure excellence in their roles. The landscape of quality management is continually evolving, and there are myriad ways to enhance your expertise and effectiveness. Here are some of the most impactful strategies for Quality Control Managers to upskill and stay competitive in the coming year:
- Embrace Data Analytics and Statistical Tools: Acquire proficiency in data analysis software and statistical tools to interpret quality metrics and drive improvements.
- Obtain Advanced Quality Management Certifications: Pursue higher-level certifications such as Certified Manager of Quality/Organizational Excellence (CMQ/OE) to deepen your expertise.
- Master Quality Management Systems (QMS): Gain comprehensive knowledge of QMS like ISO 9001 and learn how to implement and audit these systems effectively.
- Expand Lean Six Sigma Expertise: Enhance your ability to reduce waste and improve processes by advancing to higher belts in Lean Six Sigma.
- Participate in Industry-Specific Training: Attend workshops and courses that focus on the latest quality control technologies and practices in your specific industry.
- Develop Leadership and Change Management Skills: Enroll in leadership programs to better manage teams and lead organizational change initiatives.
- Network with Quality Control Professionals: Join professional associations and online communities to exchange knowledge and stay abreast of industry changes.
- Stay Informed on Regulatory Updates: Keep up-to-date with the latest regulations and compliance requirements relevant to your industry to mitigate risks.
- Implement Risk Management Practices: Learn how to identify, assess, and mitigate risks to improve the reliability of quality control processes.
- Focus on Continuous Improvement Methodologies: Adopt continuous improvement frameworks such as Kaizen to foster a culture of ongoing enhancement.
Skill FAQs for Quality Control Managers
What are the emerging skills for Quality Control Managers today?
Quality Control Managers today must master data analytics for insightful quality assessment and predictive quality maintenance. Proficiency in digital tools for quality management systems (QMS) is essential, as is an understanding of regulatory compliance in a global context. Skills in managing remote teams and cross-functional collaboration are increasingly important, along with a strong grasp of sustainable practices and the ability to integrate environmental considerations into quality protocols. Adaptability to rapidly changing technologies, such as IoT for real-time monitoring, is also a key emerging skill.
How can Quality Control Managers effectivley develop their soft skills?
Quality Control Managers can enhance their soft skills by actively engaging with cross-functional teams, which builds communication and collaboration abilities. Practicing active listening during team discussions and customer feedback sessions fosters empathy and problem-solving skills. Leadership workshops and conflict management courses can further develop interpersonal skills. Regular self-assessment, coupled with seeking constructive criticism from peers, helps in identifying areas for improvement. Embracing these strategies with a mindset geared towards continuous learning will lead to the effective development of soft skills essential for success in their role.
How Important is technical expertise for Quality Control Managers?
Certainly, Quality Control Manager skills are highly transferable. The meticulous attention to detail, process optimization, and data analysis expertise are assets in roles like operations management, supply chain management, and quality assurance consultancy. Their strong grasp of compliance standards and continuous improvement methodologies are also beneficial in regulatory affairs and risk management positions. The leadership and communication skills honed in quality control can seamlessly transition to various management-level jobs across industries, emphasizing the universal value of quality and efficiency.
Can Quality Control Managers transition their skills to other career paths?
Up Next
Quality Control Manager Education
Join our community of 350,000 members and get consistent guidance, support from us along the way
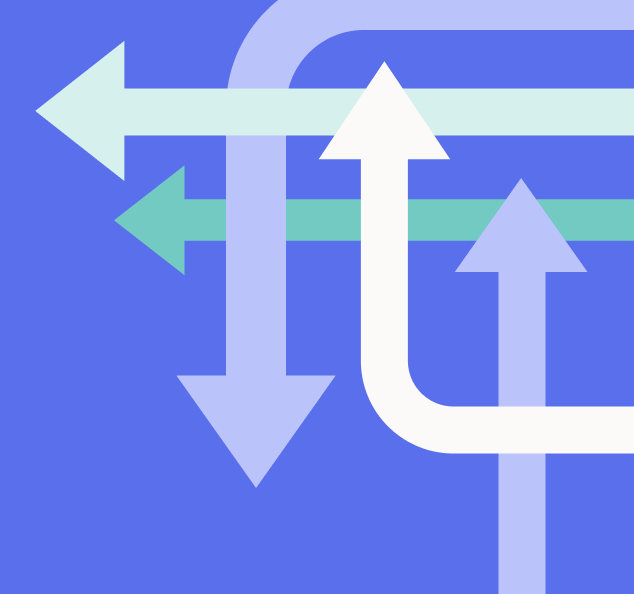